What is DCD Coating?
Richter Precision Inc. is pleased to offer our Dynamic Compound Deposition (DCD) coatings, some of the most advanced and versatile tribological coatings available anywhere. These coatings combine highly beneficial coating characteristics with processing parameters suitable for an extremely wide range of substrates. We are currently the only company in North America offering this revolutionary coating process.
Dynamic Compound Deposition (DCD) is a proprietary low temperature coating process that synthesizes dry-film lubricants and wear resistant coating compositions. DCD is based on the principle of in situ mechanical activation and chemical transformation, and leads to considerably decreased friction coefficients and increased durability of the coating layers. Due to the specific conditions of synthesis, DCD coatings develop micro- and macro-structures that are well adapted for conditions of severe contact loading. For this reason, the DCD process is primarily suited to anti-friction, slide-wear, and high-load applications.
General Characteristics of DCD Coatings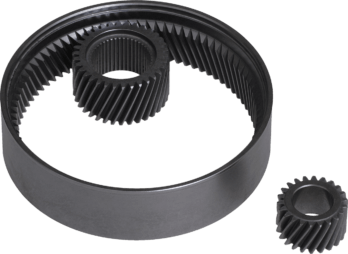
- Coatings will typically exhibit a low coefficient of friction (~0.1) depending on composition
- This is an additive process, with an average film thickness of 0.5-1.0 µm (.00002-.00004”)
- Low processing temperatures (~100°F)
- No line-of-sight limitations: process will coat wherever coating media contacts the surface
- A strong mechanochemical bond to the substrate is generated
- Suitable for any metal substrates, as well as most ceramics and plastics.
- Ideal for components with close tolerances (+/-.0001” is appropriate)
- No post-coating heat-treating is required in order to maintain core hardness
- Suitable for sharp edges: no excessive coating build-up
- Coating will generally replicate existing surface finishes, with a slight matte effect possible
Tribo-Kote™ DCD Coatings
Proprietary Name | Composition* | Color | Thickness (microns) | Micro-hardness (HV) | Coefficient of Friction | Maximum Working Temperature | Coating Process Temperature |
---|---|---|---|---|---|---|---|
Tribo-Kote™ S | (Mo, W) S2 | Gray | 0.5-1.0 | Solid Lubricant | 0.08 - 0.1 | 600°C | 38°C / 100˚F |
Tribo-Kote™ S2 | SiC / (Mo, W) S2 | Gray | 0.5-1.0 | 1000-1500 | 0.1 | 600°C | 38°C / 100˚F |
Tribo-Kote™ S3 | SiC / C-DLC | Gray | 0.5-1.0 | 1500-3000 | 0.1 | >400°C | 38°C / 100˚F |
Tribo-Kote™ S4 | Carbon DLC | Gray | 0.5-1.0 | 1500 - 2000 | 0.1 | >400°C | 38°C / 100˚F |
Tribo-Kote™ Sx | hBN** | Gray | 0.5-1.0 | 1000-1500 | 0.1 – 0.15 | >1000˚C | 38°C / 100˚F |
*- there may be some variation in coating inter-layers depending upon base materials and/or application requirements.
**- hexagonal Boron Nitride
DCD “Combination” Coatings for Stamping & Forming Applications
While our Tribo-Kote™ line of coatings work well in tribological applications, we have also had success using DCD coatings in conjunction with various PVD and CVD coating compositions. These combinations have been particularly effective in stamping and forming applications.
DCD coatings develop micro and macro-structures that are ideally suited for the conditions of severe contact loading often associated with stamping and forming applications. When a DCD coating is combined with a PVD or CVD coating, you get the wear and abrasion protection of the base coating combined with the extremely low coefficient of friction of the DCD dry-film lubricant layer. This creates a very potent combination, and can greatly improve tool life and performance in many stamping and forming applications.
PVD and CVD coatings all have a surface morphology ideally suited for DCD deposition. As it deposits onto the surface of these coatings, the DCD coating fills the micro-porosity and micro-depressions of the base films. The dry-film lubricant DCD layers that remain in these “low-lying” areas of the base PVD or CVD coating dramatically improves the overall wear characteristics of the coating.
DCD “Combination” Coatings (including but not limited to)
Proprietary Name | Composition | Color | Thickness (microns) | Micro-Hardness (HV) | Coefficient of Friction | Maximum Working Temperature | Coating Process Temperature |
---|---|---|---|---|---|---|---|
Titankote™ C2-SL+S | AlTiN-CrN/(Mo, W)S2 | Gray | 3-7 | 3200-3500 | 0.15 | 1000°C / 1832°F | 375°C / 707°F |
Titankote™ C3+S | CrN/CrC/(Mo, W) S2 | Gray | 3-7 | 2000-2200 | 0.15 | 700°C / 1292°F | 375°C / 707°F |
Titankote™ C6+S | AlTiN / (Mo, W) S2 | Charcoal | 3-7 | 3000-3400 | 0.15 | 900°C / 1652°F | 375°C / 707°F |
Titankote™ H+S | TiC / (Mo, W) S2 | Gray | 4-12 | 3200-3400 | 0.15 | 600°C / 1112°F | 1050°C / 1925°F |